Polietilen Teraftalat
Polietilen teraftalat, Avrupa'da ambalaj sektöründe birçok nedenle en yaygın şekilde kullanılan plastiklerden birisidir.
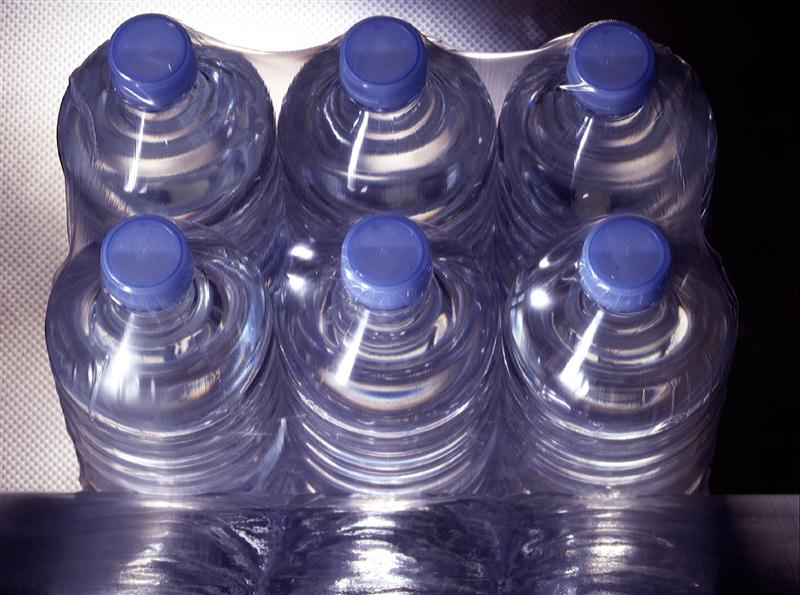
- Geçmiş
- Özellikler
- Uygulamalar
- Süreçler
- Geri Dönüşüm
- SSS
Geçmiş
PET, ilk defa yeni tekstil lifleri üretmeye yarayacak bir polimer araştırılırken DuPont kimyagerleri tarafından sentezlenmiştir, ancak çok uzun zincirler elde etmeyi mümkün kılan teknoloji ICI (Imperial Chemical Industries) tarafından 1941 yılında geliştirilmiştir. Polyester lif uygulamaları geliştirilmiş, PET polimeri 1990'ların sonu itibariyle dünya geneli sentetik lif üretiminin %50'sini oluşturmuştur. Tek başına yahut pamuk ve yün ile beraber kullanıldığında yıkamaya/aşınmaya karşı ve buruşmaya karşı daha iyi direnç gösterir, lif hali `Dacron´ ya da `Trevira´ olarak bilinir.
1950'lerin sonlarında, ince ve ekstrüde edilen bir plakanın iki yönlü esnetilmesiyle elde edilen bir film halinde geliştirilmiştir. Bu haliyle PET film video, fotoğrafçılık, x-ray film ve ambalajlarda yaygın bir kullanım alanı yakalamıştır.
1970'lerin başlarında, belli bir biçime sahip bir kalıp içerisinde bir balonu şişirir gibi, hava basınçlı kalıplama yoluyla üç yönde esneme sağlanarak şişe tipi ilk kaplar üretilmiş, PET kullanılarak cam şişenin yerini alacak hafif, sert, kırılmaz bir malzeme elde edilmiştir.
Özellikler
Daha önce bir plastik şişeden gazlı içecek, su ya da meyve suyu içmişseniz, bu şişe büyük ihtimalle PET veya polietilen tereftalattan üretilmiştir.
PET, Avrupa'da ambalaj sektöründe birçok nedenle en yaygın şekilde kullanılan plastiklerden birisidir. Yüksek basınca dayanıklıdır ve yere düştüğünde patlamaz. Gaz kaçırmayan özelliktedir, bu nedenle gazlı içeceklerin gazını içeride tutar ve şişelenmiş içeceklerin lezzetini korur.
Uygulamalar
PET'in kullanım alanlarından bazıları şunlardır:
- Alkolsüz içecekler, meyve suları, maden suları gibi içecekleri içeren şişeler Özellikle gazlı içecekler, yemek ve salata yağları, soslar ve deterjanlar için uygundur.
- Geniş ağızlı kavanozlar ve reçel kapları, konserveler, meyveler ve kurutulmuş gıdalar
- Mikrodalga veya normal fırınlarda yeniden ısıtılabilen önceden pişirilmiş yemek tepsileri Makarna yemekleri, et ve sebzeler.
- "pakette haşlanan" önceden pişirilmiş yemeklerde kullanılan folyolar, atıştırmalık gıdalar, fındıklar, tatlılar, uzun ömürlü şekerlemeler.
- Ekstra oksijen bariyeri olan diğer PET ürünler ise bira kutuları, peynir gibi vakumla paketlenmiş süt ürünleri, işlenmiş et, `kutu içi torba´ şaraplar, baharat, kahve, pasta ve şuruplar için kullanılabilir.
Süreçler
PET için kullanılan hammaddeler, diğer pek çok plastikte olduğu gibi "ham petrolden" çok sayıda petrol ürününün ortaya çıktığı damıtma ve ayırma işlemleri sonrası elde edilmektedir. Bu işlemlerden sonra iki PET ara ürünü veya monomeri elde edilir, saflaştırılır ve geniş, sızdırmaz bir "pişirme kazanı" tipi kapta karıştırılır, yavaş yavaş azalan basınç altında 280-300°C'a kadar ısıtılır. Reaksiyonda bu ara ürünlerin her birinin birbirine benzer iki noktası bulunur, dolayısıyla birçok molekülü birbirine bağlayarak ve monomerlerin ester bağlarıyla birbirine bağlandığı bir polimer yaratarak zincirler oluşturabilir.
Reaksiyon ilerledikçe bu karışım daha akışmaz bir hal alır ve nihayetinde uygun akışmazlığa ulaşıldığında reaksiyon durur. Bu aşamada, PET reaktörden ince "spagettiye benzer" teller halinde ekstrüde edilir, suya sokularak derhal soğutulur, boyama ve diğer işlem aşamalarına iletim öncesi küçük şeffaf granüller yahut pelletler haline getirilir. Kola şişelerinin üretiminde kullanılan PET malzeme, katı granüllerin erime noktaları altında ısıtılmasıyla bir kez daha damıtılır, bu sayede bazı impüriteler giderilerek malzemenin fiziksel özellikleri iyileştirilmiş olur.
Geri Dönüşüm
Bir malzeme olarak büyük ölçüde geri dönüştürülebilen PET, AB direktifinde plastikler konusunda işaret edilen geri dönüşüm hedeflerinin karşılanmasına devasa ölçüde katkı sağlar. PET malzeme geri dönüştürülemediğinde, enerji geri kazanımı sağlamak üzere yakılabilir.
Ayrıca PET malzemede, genelde ağır metal ve/veya çevreye zararlı maddeler bulunmaz.
Temiz yıkama işlemlerinden geçerek polimer pullarına dönüştürülen (mekanik geri dönüşüm) veya kimyasal işlemle parçalanarak oligomer yahut başlangıç polimerleri olan tereftalik asit ve etilen glikol elde edilen (kimyasal geri dönüşüm) PET geri kazanılabilir, malzemeler yeniden kullanılabilir, Daha sonra bu ara ürünler saflaştırılır, yeniden polimerleştirilirek yeni PET reçineleri elde edilir. Geri dönüşüme uygun olmayan (örneğin çok kirli veya temizlenemeyecek kadar kirlenmiş) PET atıklar için en son çözüm yakılarak enerji elde edilmesidir.